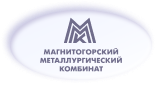
10236
Диагностика оборудования и прогнозирование неисправностей
Февраль, 2020 год.Система предиктивной диагностики электродвигателей ПТК «Мониторинг-Предиктив».
Какую проблему решали
Для контроля состояния электромеханического оборудования — электродвигателей, насосов, редукторов — на объекте постоянно присутствовал технический персонал, еженедельно проводились плановые выезды бригад.
В случае сбоя в работе оборудования специалист по вибродиагностике проверял среднеквадратичные значения отклонений ошибки от нормы и делал предположения по возможным неисправностям.
В случае сбоя в работе оборудования специалист по вибродиагностике проверял среднеквадратичные значения отклонений ошибки от нормы и делал предположения по возможным неисправностям.
Введение в эксплуатацию резервного оборудования и ремонт вышедших из строя агрегатов занимали много времени, что приводило к длительному простою и большим издержкам.
Решение проблемы
Команда МАК «Вымпел» внедрила на предприятии ПАО «Магнитогорский металлургический комбинат» программно-технический комплекс «Мониторинг-Предиктив», который контролирует работу электромеханического оборудования в процессе его эксплуатации.
Беспроводные датчики измеряют электромагнитное поле электродвигателей и их вибрацию. Полученные данные передаются в систему, которая быстро и точно определяет наличие и тип неисправностей и заблаговременно прогнозирует возможные дефекты составных частей электродвигателя.
Процессы технического обслуживания и ремонта (ТОиР) электромеханического оборудования переведены из режима плановых ремонтов на обслуживание по состоянию, что существенно снижает затраты на его содержание.
Применяемые технологии
Программно-технический комплекс «Мониторинг-Предиктив» — первое решение на российском рынке, которое проводит анализ состояния электродвигателя по электромагнитному полю.
Исходные данные для диагностики — вибрация составных частей оборудования и магнитное поле электродвигателя. Данные по беспроводным каналам связи поступают на сервер, где осуществляется их обработка, выявление дефектов и прогнозирование работы.
Технология предсказания износа и выхода из строя агрегатов построена на методах кластеризации и машинного .
Для классификации неисправностей применялась нейронная сеть на базе многослойного персептрона, которая содержит 15 входных нейронов, по числу основных дефектов.
Бизнес-процесс
До проекта:
- До 20 дней уходило на диагностику и выявление неисправностей электродвигателя.
- Постоянное присутствие ремонтной бригады на объекте.
- Бумажный журнал выявленных проблем и аварий.
- Большие издержки на обслуживание оборудования.
- До 2 месяцев на плановый ремонт оборудования.
После проекта:
- Автоматический контроль работы оборудования.
- Прогнозирование возможных неисправностей.
- Планирование затрат на сервис, производство и закупки.
- Переход от плановых ремонтов к ремонтам по состоянию.
- Сокращение затрат на ТоиР.
- Автоматизация процесса закупки материалов для ремонта.
Результаты
Команда ММК
Денис Якобчук
Директор ООО «РНД МГТУ»
Команда МАК "Вымпел"
Андрей Ершов
Начальник управления продаж и развития гражданской продукции
Евгений Ишметьев
Советник
Алексей Митиогло
Заместитель генерального директора по экономике и финансам
Сергей Пырко
Главный конструктор
Похожие кейсы
AI-кейсы с доказанной бизнес-эффективностью. Все проекты успешно прошли проверку комиссией из признанных экспертов в технологиях и бизнесе.